
Maintenance Tips for Double-Acting Welded Hydraulic Cylinders
Hydraulic Cylinders Maintenance Tips Industrial Equipment Leak Detection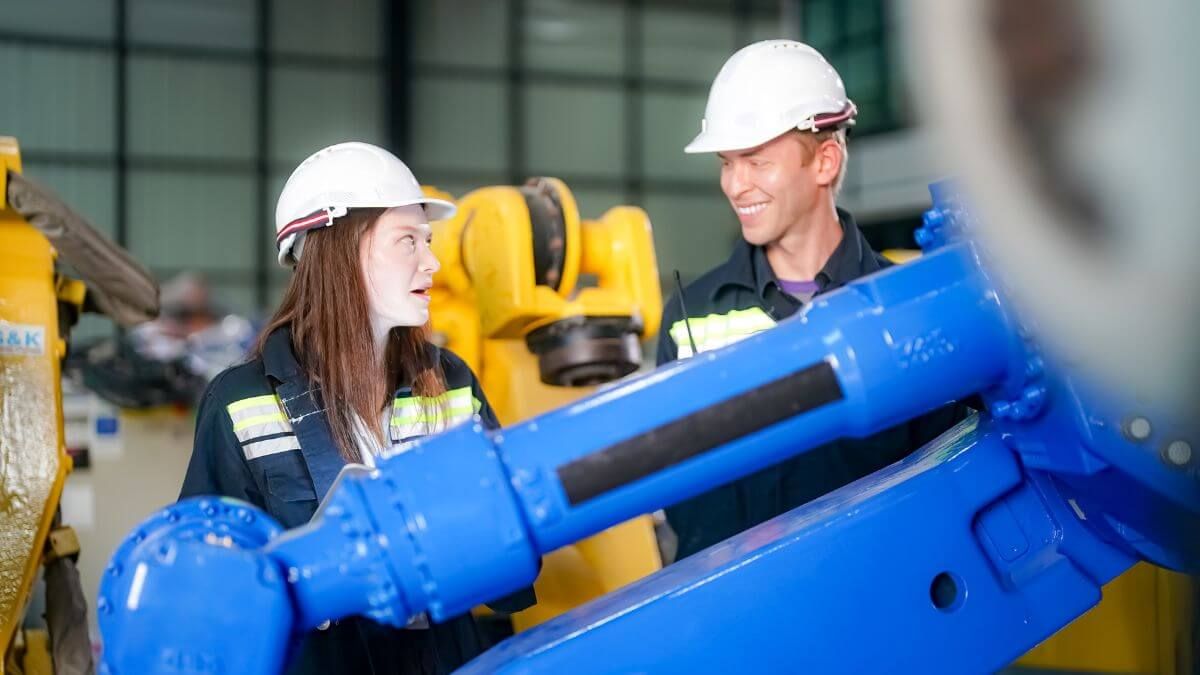
Double-Acting Welded Hydraulic Cylinders Double-acting welded hydraulic cylinders are essential components in many industrial and mobile applications, providing force and movement necessary for operating machinery efficiently. As such, regular maintenance of these cylinders is key for their longevity, reliability, and performance - here are some helpful maintenance tips that can keep them operating at optimal performance levels for years.
Regular Inspection
An Essential Step Its Conducting regular inspections is an integral component of maintaining double-acting welded hydraulic cylinders, as it identifies potential issues before they cause costly repairs or downtime. Here's a detailed guide on what you should inspect during these regular checks as well as solutions to common problems that may be found during them. Key Areas to Inspect
Cylinder Rod Surface Condition: When inspecting cylinder rods for surface damage such as scratches, pitting, corrosion or any other form of impairment it's important to look out for any evidence of scratches, pitting or corrosion as damaged rods may lead to rapid seal wear and fluid leakage issues.
Straightness: For optimal performance, check that the rod is straight and not bent. A bent rod may lead to misalignment that leads to uneven wear and eventual failure, as well as inspection for wear or damage in its connection points with loads or machines.
Rod Ends: Before inspecting any rod ends that attach to loads or machines for wear or damage at connection points where loads or machines connect directly with it.
Action: If any damage is discovered, polish minor scratches with fine emery cloth to repair minor damages or bends in the rod. In cases of more extensive or severe damage or bends, replacement may be necessary.
Seals and Gaskets Worn and Teared: Check for signs of wear, cracking or deterioration in seals and gaskets to maintain hydraulic pressure and avoid leaks. Ultimately these components play an essential role in maintaining hydraulic pressure.
Leaks: Check for hydraulic fluid leakage around seal areas to detect even minor leaks that indicate worn or damaged seals that need replacing immediately, and replace any that appear worn out or damaged immediately to maintain system integrity and ensure its continuity. In terms of materials compatibility with your hydraulic fluid and operating conditions, ensure seal replacement promptly in order to preserve system integrity.
Cylinder Barrel's Exterior Condition: Carefully inspect the outside of your cylinder barrel for signs of physical damage such as dents, cracks or corrosion to ensure its longevity and performance. Any physical damages can have detrimental impacts on both performance and lifespan of your cylinder.
Interior Condition: If possible, inspect the interior surface for signs of wear or scoring during more intensive maintenance or when disassembling the cylinder. This should typically occur as part of more in-depth maintenance or when disassembling it entirely.
Action: If there is significant damage, repair or replace the barrel immediately. Applying protective coatings regularly may help protect against exterior corrosion.
Mounting Points
Hardware Condition: Inspect all mounting hardware such as bolts, nuts, and brackets for tightness as well as any signs of wear or damage to ensure proper function and alignment with the cylinder. Loose or worn mounting hardware could result in misalignment and increase wear on its components, possibly leading to misalignment and premature wear on your cylinder.
Align: Align the cylinder correctly with its load and other system components for optimal performance and efficiency. Misalignment may lead to uneven wear and decrease efficiency.
Action: Tighten or replace any loose or damaged hardware as soon as possible and use alignment tools to verify its proper placement of the cylinder. Hoses & Connections
Condition of Hoses: Inspect hydraulic hoses for signs of wear, cracks or leaks that could lead to fluid loss and lower system performance. Connections: All connections should be checked for tightness and any leaks to ensure secure connections that do not become damaged over time.
Action: Replace damaged hoses and secure all connections tightly and securely, using appropriate sealants on fittings to avoid leaks. FREQUENCY OF INSPECTIONS
Inspection frequencies should depend upon operating conditions and usage frequency for your hydraulic cylinders:
Heavy-Duty Use: When inspecting cylinders used in harsh environments or heavy duty applications, more frequent inspections may be necessary - typically weekly or bi-weekly inspections.
Moderate Use: Monthly inspections may suffice.
Light Use: Cylinders used occasionally or for light duty applications may only require annual inspection.
Documentation and Record-Keeping
Maintaining detailed records of your inspections can help keep an accurate account of their condition over time and identify recurring problems with hydraulic cylinders. Document the following items during each visit: *Station Date/Inspection Number/Operators for Each Visit,
Condition: Document the condition of each component that was inspected. Maintenance/Repair Actions Taken: Detail any maintenance or repairs performed on the cylinder, and record what maintenance/repair measures were undertaken. Next Inspection Date: Arrange an inspection based on its condition and usage needs.
Establish Proper Lubrication
Proper lubrication of double-acting welded hydraulic cylinders is critical to their smooth operation and long term success, helping reduce friction, wear, and ultimately improving system efficiency. Here is an in-depth look at how you can maintain proper lubrication for your hydraulic system cylinders.
Importance of Lubrication
Reducing Friction: Lubrication decreases friction between moving parts within a cylinder, such as piston and barrel, to minimize wear-and-tear and extend their lives.
Dissipation: Effective lubrication helps dissipate heat generated during operation, helping prevent overheating and damage to the cylinder.
Corrosion Prevention: Lubricants provide a protective barrier that keeps moisture and contaminants out of metal surfaces, thus decreasing corrosion risk.
Seal Protection: Lubrication helps preserve seal flexibility and integrity, reducing leaks while keeping pressure within hydraulic systems at its required levels. Key Lubrication Practices (KLPs)
Lubricate Cylinder Rods and Seals
Regular Application: Apply a thin film of lubricant to the cylinder rod regularly in order to reduce friction and protect seals, particularly if operating in dusty or dirty environments. This practice will reduce wear-and-tear and prolong its usefulness.
Type of Lubricant: Choose a silicone- or petroleum-based lubricant compatible with both the hydraulic fluid and materials of seals and rods. Silicone is often preferred but alternative solutions exist as well.
Action: Schedule regular lubrication according to operating conditions; more frequently for those exposed to harsh environments or with frequent usage. for hydraulic fluid maintenance see here
Check Fluid Levels Regularly: Be sure to regularly inspect the hydraulic fluid levels in your reservoir, as low levels could result in inadequate lubrication and increased wear on machinery.
Fluid Quality: To protect cylinders and other hydraulic components from possible harm caused by contaminants in hydraulic fluid, be certain that its quality remains clean and free from contaminants. Contaminations in the fluid could potentially wreak havoc with its performance and lead to irreparable damage if left contaminated for too long.
Action: Refill hydraulic fluid as needed and change it periodically according to manufacturer recommendations for maximum performance. Choose high-grade fluid to ensure the best outcome.
Filtration Systems
Hydraulic systems should incorporate filters to remove contaminants from their fluid. Be sure to regularly replace and inspect these filters so as to maintain fluid cleanliness.
Filtration Quality: Confirm that the filtration system meets your specific application. Fine filters can remove smaller particles, decreasing contamination risks. Action: Create a schedule for checking and replacing filters depending on operating environment and system usage.
Monitoring Lubrication Effectiveness Performance Monitoring: Keep an eye on how well your hydraulic cylinders are performing, especially increased friction or unusual noises that slow operation may signal lubrication issues.
Temperature Monitoring: Utilize temperature sensors to track heat generated by your cylinders, as excessive heat could indicate inadequate lubrication practices. Action: Assess any performance issues or temperature spikes immediately and adjust lubrication practices as necessary for optimal operation.
Choose Hydraulic Fluid with Care
Compatibility is Key: Select hydraulic fluid compatible with the seals and materials on your cylinder to avoid swelling, hardening or degradation to seals. Incompatible fluids could result in seal failure.
Viscosity: Select a fluid with an appropriate viscosity for your operating conditions, such as selecting higher viscosity fluids that provide better lubrication but may require additional energy to pump.
Action: Referring to your cylinder manufacturer's recommendations regarding recommended hydraulic fluid types and viscosities is recommended; once selected, select according to individual application needs.
Environment Considerations
Dust and Dirt: For environments with high concentrations of dirt and dust, consider employing dust wipers and extra protective seals to keep contaminants away from the cylinder rod and seals.
Humidity and Moisture: For humid or damp environments, use lubricants with corrosion inhibitors to protect cylinder components from rusting or corrosion. Action: Implement additional protective measures based on environmental conditions where cylinders operate.
Assess Hydraulic Fluid Quality
Hydraulic fluid is the backbone of any hydraulic system, playing an indispensable part in its operation and longevity of double-acting welded hydraulic cylinders. Assuring your system runs efficiently requires monitoring its quality to prevent damage or costly downtime - here's a complete guide on how to monitor and maintain this essential resource for smooth functioning - here is also included a section dedicated to Hydraulic Fluid Quality Quality is Important to Us
Lubrication: High-grade hydraulic fluid provides crucial lubrication, reducing friction and wear on moving parts, as well as heat transfer through its use to help dissipate heat generated during operation, maintaining optimal temperatures levels while avoiding overheating.
Contamination Control: Clean hydraulic fluid protects systems from harmful contaminants that could lead to wear, corrosion and blockages in the system. System Efficiency: Proper fluid quality ensures proper system pressure and performance and that hydraulic cylinders operate optimally.
Monitoring Hydraulic Fluid Quality with Key Practices
Take Regular Fluid Sampling
Inspect Your System Regular fluid sampling from a hydraulic system is highly recommended to maintain peak performance in terms of both operating conditions and usage intensity; heavier-duty or critical applications require more frequent samples for better monitoring of performance.
Sampling Points: Take samples at various points throughout your system - such as reservoir, pump and return lines - in order to gain a comprehensive view of fluid condition across it all. Step: Develop a routine fluid sampling schedule in order to collect samples on a consistent basis.
Fluid Analysis
Contaminant Detection: Analyze fluid samples to detect contaminants such as dirt, metal particles, water and air that could indicate wear, leaks or other issues within your system.
Viscosity Check: Evaluate the viscosity of hydraulic fluid. Changes in viscosity may interfere with its ability to lubricate and dissipate heat efficiently, thus impairing performance and functionality.
Additive Levels: Evaluate the levels of additives present in your fluid, such as anti-wear agents, corrosion inhibitors and antifoaming agents. Depletion of such additives can compromise fluid performance.
Step: Utilizing professional fluid analysis services or on-site testing kits, analyze fluid samples. Examine their results for any deviations from acceptable levels.
Filtration Systems
Filter Condition: Regularly check and replace hydraulic filters to maintain peak filtration performance and avoid any unwanted debris entering the system, potentially causing irreparable damage. Filters remove contaminants from fluid circulation by trapping them within a filtering media layer that removes them before they contaminate further systems or cause more issues in future use.
Filter Type and Replacement Frequency: Ensure the filters you are using are suitable for the system in terms of removing contaminants of various sizes and types. Actions: Implement an inspection/replacement schedule consistent with manufacturer recommendations and operating conditions.
Water Contamination Control
Water Ingress: Prevent water from entering your hydraulic system as this can cause corrosion, reduce lubrication efficiency and ultimately lead to the formation of sludge. Dehydration: Utilize filters or dehydration units equipped with water-absorbing materials in order to remove any unwanted moisture that has entered.
Action: For best results, regularly monitor for signs of water contamination such as cloudy fluid and take corrective actions to eliminate it.
Maintain Optimal Temperature Temperature Monitoring: To ensure optimal operating temperature of hydraulic fluid, constantly monitor its operating temperature. Excessive heat may degrade fluid quality and lead to oxidation while low temperatures may increase viscosity and decrease performance.
Cooling Systems: Make sure the cooling components in your hydraulic system, including heat exchangers and coolers, are functioning optimally. Action: Use temperature monitoring devices to keep an eye on fluid temperature levels so they remain within recommended parameters.
Addressing Fluid Degradation
Oxidation and Acid Formation: Be on the lookout for signs of fluid oxidation or acid formation due to high temperatures or contamination; this could result in corrosion or sludge formation and must be addressed as quickly as possible.
Fill with high-quality hydraulic fluid for refills as per manufacturer guidelines for replacement intervals and refill intervals. Ultimately, to maintain its properties and performance capabilities, hydraulic fluid should be periodically replaced according to its manufacturer's recommendations for refill intervals and use high-grade, compatible fluid refills for refills.
Test for Leaks
It is crucial to your system efficiency, safety and longevity that double-acting welded hydraulic cylinders are regularly checked for leaks in order to maintain system efficiency, safety and longevity. Hydraulic leaks can result in pressure loss, reduced performance and potential system components becoming damaged - here's an in-depth guide on how and when to check for them and what actions to take if found. Importance of Leak Detection
System Efficiency: Leaks decrease overall hydraulic system efficiency by draining away fluid and pressure, as well as creating slippery surfaces which pose safety threats to operators and maintenance staff. They may even create dangerous situations for them when operating machinery.
Component Longevity: Leaks can reduce component longevity by insufficiently lubricating, increasing wear, and potentially leading to their failure.
Environmental Impact: Hydraulic fluid leaks have the potential to pollute the environment and require expensive cleanup costs or regulatory fines as a result.
Key Steps for Leak Detection
External Leaks: Conduct a careful visual inspection of the hydraulic cylinder, hoses, fittings and connections in your system for any visible signs of hydraulic fluid on their exterior surfaces.
Common Leak Points: Be particularly vigilant of places where leaks may form, such as seals, gaskets, hose connections and mounting points.
Action: Utilize a bright light to inspect difficult-to-see areas while cleaning any dirty surfaces to make leaks easier to detect.
Pressure Testing
A static pressure test should involve pressurizing your hydraulic system while it remains stationary, monitoring pressure gauges for any changes which might indicate leaks.
Dynamic Pressure Test: Conduct a dynamic pressure test by operating your hydraulic system under normal working conditions and checking for pressure fluctuations that might indicate leaks in its hydraulic system.
Action: For optimal testing results, calibrated pressure gauges must be utilized and system pressure is brought up to its normal operating levels during testing.
Use of Leak Detection Fluid
Apply leak detection fluid or dye directly into your hydraulic system in order to easily identify leaks. These fluids typically change color under ultraviolet lighting, making it easy for leak detection professionals to spot them more easily.
Application Areas: Apply detection fluid around seals, fittings and any potential leak points before operating the system briefly to allow any potential leak paths for penetration by the fluid. Action: To inspect after applying detection fluid use UV lighting as you inspect with an examination light before cleaning the area thoroughly afterwards.
Seal Inspection and Replacement
Regularly check seals and gaskets for signs of wear, cracking or deterioration as worn seals can often lead to leakage in hydraulic systems. Any damaged or worn seals should be promptly replaced in order to stop any future leaks from forming or worsening.
Action: For optimal operation of your system, ensure that high-quality seals match both its hydraulic fluid and operating conditions. Hosiery Maintenance and Fitting Maintenance
Hose Inspection: When performing scheduled hose and fitting maintenance inspections, inspect hydraulic hoses regularly for wear, cracks or abrasions which could allow pressure leakage into damaged sections resulting in leakage or burst under pressure.
Tightness of Fittings: Ensure all fittings are securely tightened without over-tightening as this can damage threads and cause leaks.
Action: Replace any damaged hoses as soon as possible and tighten fittings using torque specifications appropriate to their type.
Monitoring and Logging
Keep a Leak Log: Create and keep track of any leaks detected, their locations, severity and the corrective actions taken as this helps identify recurring issues or areas needing closer monitoring.
Regular Checks: Establish a regular inspection and maintenance management system to track inspections and repairs for leakage checks on systems with high usage or pressure levels, particularly those subject to frequent use or pressure fluctuations.
Action: Utilize this system for tracking leak checks regularly and consistently over time.
Promptly Address Leaks
Immediate Action is Needed: Take immediate steps to address detected leaks to minimize further damage and fluid loss, since smaller leaks can quickly grow larger without proper care being taken.
Root Cause Analysis: Establish the cause of the leak by identifying factors like seal wear, loose fittings or damage to hoses that might contribute.
Corrective Actions: Take appropriate actions based on root cause analysis to prevent future instances of the same issue from reoccurring.
h1 Establish Proper Alignnement
It is vital that double-acting welded hydraulic cylinders are aligned correctly for efficient and long-term operation, since misalignments may lead to excessive wear, reduced efficiency, or premature failure of all connected components. Here's a detailed guide on ensuring appropriate alignment for your hydraulic cylinders. Importance of Alignment for Hydraulic Cylinders.
Reduce Wear and Tear: Proper alignment reduces uneven stress on cylinder rods and seals, thus minimizing wear and tear. Enhance Efficiency: Cylinders operating smoothly enhance overall system efficiency.
Extension of Lifespan: By ensuring proper alignment, misalignment can extend the lifespan of hydraulic components such as cylinders and other hydraulic parts, thus reducing maintenance costs and downtime. Safety: Proper alignment ensures safe operation by minimizing risk for unexpected failures or accidents during operation. Steps for Ensuring Proper Alignment
Aligning during Installation
Mounting Surface: For optimal alignment from the start, ensure the mounting surfaces for your cylinder are level and free from debris or irregularities - this helps achieve proper alignment from day one.
Parallelism: Make sure that both mounting points for both ends of a cylinder are lined up perfectly parallel. Any deviation can cause wear-related problems within the rod and ultimately increase wear costs.
Action: For optimal installation results, utilize precision tools such as a level and straightedge to check the surface flatness and parallelism during assembly.
Centerline Alignment Axial Alignment: For proper functioning of a cylinder, ensure its centerline is in line with both load direction and movement path. Misalignments can result in side loading which places undue stress on rods and seals of the cylinders.
Avoid Side Loading: Avoid side loading of the cylinder rod by using alignment jigs or fixtures to maintain centerline alignment during installation and adjustments. Sideloading occurs when loads don't align properly with its centerline, creating uneven forces. Instances include loads that don't follow its centerline and produce unequal forces as a result. To protect yourself against such sideloading issues use alignment jigs/fixtures during these processes for centerline maintenance during installation and adjustments.
Consistent Alignment Checks/Visual Inspection: On an ongoing basis, inspect the cylinder and its mounting points for signs of misalignment such as uneven wear on its rod or seals, as this could indicate misalignment issues that require adjustment.
Measuring Tools: For precise alignment measurements, dial indicators, calipers or laser alignment tools may help. These instruments can detect misalignments that may not be visible to the naked eye.
Action: Implement periodic alignment checks as part of your scheduled maintenance to ensure proper alignment over time.
Adjusting Align Whilst Employing Shim Adjustments: If misalignment is detected, use shims to correct slight misalignments at mounting points and ensure smooth functioning of your cylinder. Shims will help correct minor discrepancies while helping ensure smooth cylinder operation.
Mounting Adjustments: Align the mounting brackets or bolts so they are in correct alignment, taking care that all adjustments are even and do not cause misalignments. Handeln Action: For accurate alignment, make small incremental adjustments at a time until all have been tested thoroughly to achieve precise positioning.
Consider Spherical Bearings
Spherical Bearings can provide the solution to misalignments at mounting points by serving as pivot points to allow movement in multiple directions.
Flexible: Spherical bearings offer considerable flexural tolerance to accommodate minor misalignments without stressing cylinder rods or seals, decreasing wear and extending component lifespan.
Action: Consider using spherical bearings when perfect alignment is difficult or there is significant movement.
Proper Support for Long Strokes
Intermediate Supports: Cylinders with long strokes should use intermediate supports to avoid sagging and ensure alignment across their entire stroke length.
Guide Rails or Supports: Install guide rails or supports to maintain alignment during operation of the cylinder rods. Action: To maintain optimal performance of long stroke cylinders, ensure adequate support structures exist that ensure their continued alignment.
Dynamic Applications
Aligning Movement Path: When working dynamically, ensure that the load path and movement path remain aligned during operation to prevent misalignments caused by load path shifts or movements during use of the cylinder. Misalignments could arise if either moves during its cycle.
Flexible Connections: Use flexible hose connections to allow movement without misalignment from rigid pipes.
Action: Regularly monitor dynamic applications to ensure alignment is maintained across their full range of motion.
Prevent Corrosion
Corrosion can significantly shorten the lifespan of hydraulic cylinders in harsh environments. To combat corrosion effectively, use cylinders with protective coatings or finishes which resist it.
Environmental Protection: Shield hydraulic cylinders from exposure to harmful elements such as moisture, chemicals and salt. For best results when not in use, store hydraulic cylinders in an environment free from moisture and dust to minimize corrosion risk. 7. Perform Routine Maintenance Tasks
Routine maintenance tasks can help ensure small issues do not escalate into major ones.
Seal Replacement: For optimal functioning of the hydraulic system, regularly replace seals and gaskets.
Component Inspection: Regularly disassemble your hydraulic cylinder to inspect internal components such as piston, rod, and barrel for wear or damage.
Tip: For best results, follow your manufacturer's maintenance schedule guidelines for your specific hydraulic cylinders.
Conclusion Proper maintenance of double-acting welded hydraulic cylinders involves regular inspections, proper lubrication, monitoring hydraulic fluid quality, checking for leaks and alignment issues as well as protecting against corrosion - along with routine maintenance tasks to extend their lifespan, improve performance and avoid costly downtime. By following these tips you can extend their lives, enhance their performance and eliminate costly downtime altogether.